Stainless steel sinks can be made using two processes. They might be stamped, or they could be hand-made. The production processes for each of these kinds of sinks are unique. In this article, we will talk about the production method used to make a press sink. This is also known as a drawn sink, and you will see both naming conventions used for this kind of sink.
There are different thicknesses of stainless steel that are used to make these sinks, and you will want to be sure that you are getting the quality of sink that you need. You will want to be sure that you check on the thickness of the metal that is used for this kind of sink, as this can impact the longevity of the sink as well as its overall functionality.
Manufacturing Process
1. Sheet Metal Cutting
The sheet metal used to make sinks is typically between 0.8 and 1.5 mm thick. This is an ideal thickness for this sink and makes for the best results. The sink factory will have various steel plates of differing thicknesses used for the production of sinks. They will select from the various thicknesses when completing sink products for different functions and uses.
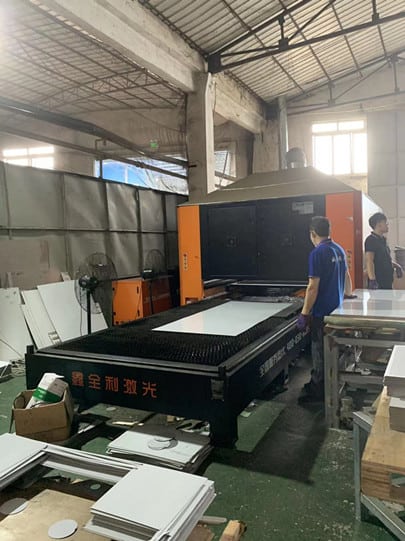
The sheet metal is delivered to the factory in coils by weight, and the width of the sheet is usually 1220 mm. The length could be unlimited. This is the material that is pressed, or drawn, to make each sink.
2. First-Time Drawing
The metal is put on the drawing press machine and drawn through the upper and lower laminated plates that make up each workbench. The product mold is in the opening in the workbench. A machine presses the worktable into the mold until the steel plate is forced through the shape of the mold. The goal at this juncture is to make the first drawing depth about 80% of the total design depth.
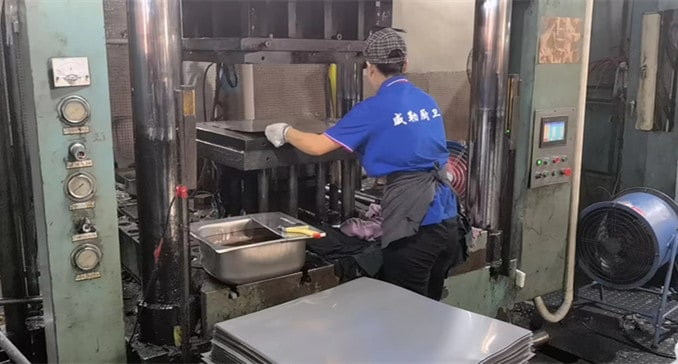
The sink them have to be cleaned after this part of the process so that the drawing oil that is used to make the process effective is removed. This must be done in between various stages of the process of pressing a sink to make sure that each step is successful.
3. Annealing
Annealing restores the stainless steel’s strength which was impacted by the first drawing process. This is done on another assembly line which is usually not very long. The sink products are run through a furnace that is heated to about 1150 degrees C. The sinks are moved through this part of the process with a crane lock or a conveyor belt.
This step also demagnetizes the sink so it will not attract metal objects. This step is not always done in-house, and many companies send out their sinks to be annealed. It is more efficient to do this part of the process in-house, but not all factories can do so.
4. Second Time Drawing
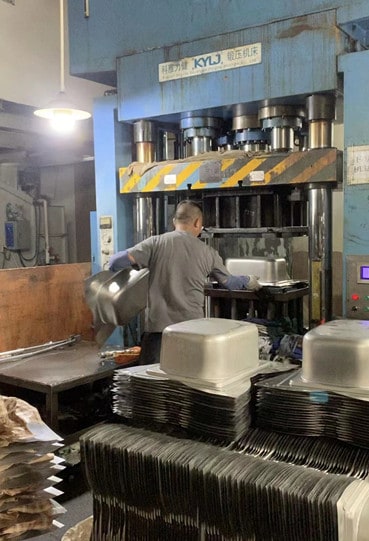
The process of drawing the sink is repeated. This time it is done with a mold and hydraulic press. This is to create the design depth. The first drawing was just to create the shape of the sink. This is the drawing that refines the sink and makes it useful.
5. Trimming
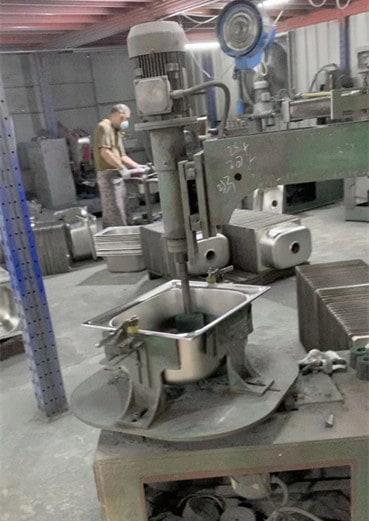
After the second time drawing the sink, there will not be any shrinkage on the edge of the steel sheet. This is when the excess trim is taken off the now-finished product. This process is often checked by hand, or it might even be done by hand in some factories.
6. Hole Punching
What would a sink be if it did not drain? When the sink has been drawn the second time and trimmed, it is then sent to the punching machine. This is the machine that punches out the drain hole and the other holes that are necessary for handles and the spigots to be installed. This process might be cleaned up by hand to remove any burrs left behind when the cutting is done. Some factories have a machine that cuts cleanly and does not leave any burring.
7. Surface Treatment
Different surface treatments can be applied to the sink to finish its surface. Most sink manufacturers will do the same four steps when they are doing the surface treatment step of the sink’s finish work.
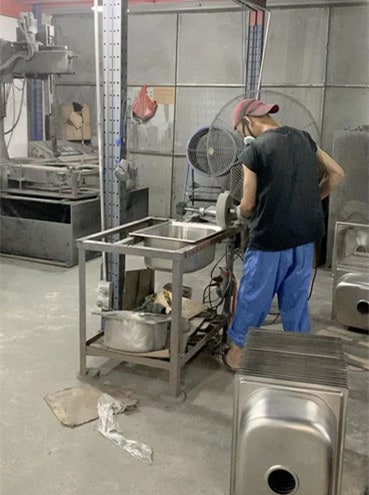
- Sanding is done to smooth the surface of the sink and to smooth the underside as well.
- Grinding is completed to remove burrs and to modify some of the surfaces for different kinds of receptacles. This is done with a grinding wheel that can smooth the vertical faces as needed.
- The sink is polished to create a smooth finish
- Embossing is done to mark the sink with the manufacturer’s name.
8. Spray Coating
The spray coating step protects the bottom of the sink from damage and visible imperfections. This layer of material is lightweight and covers the traces that are left over from the annealing process. It also prevents condensation in the kitchen when the sink is in use.
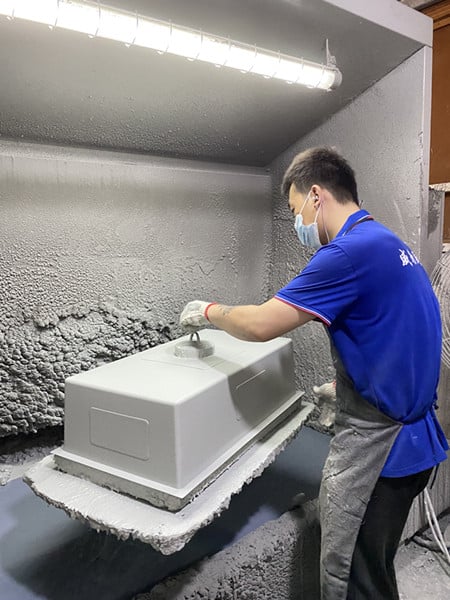
9. Cleaning and packing
This stage removes any residual drawing oil and any dust or grime still stuck to the sink and verifies that all the steps of the sink creation process are complete. The sinks can then be packed into brackets, large boxes, or other kinds of retail packaging depending on the delivery method that is set to be used for the shipment.
Chica Stainless Steel Sink
If you are looking for a quality drawn stainless steel sink, you need to work with Chica sink to get the products you need. Chica makes high-quality stainless steel sinks that are made to last and are crafted with precision and attention to detail. Getting quality sinks matters, and you can be sure you will get the right sinks for your needs from Chica.